價值流圖在車間生產周期分析的應用
日期:2017-05-31 / 人氣: / 來源:www.ambgjj.com / 熱門標簽:
最近接觸的幾個客戶都強調要將價值流管理單獨作為一個咨詢主題,然而接觸下來發(fā)現(xiàn)客戶多半是未理解價值流圖的用處和局限性??蛻粝M膬r值流分析是一個包含企業(yè)運營管理全流程的診斷,系統(tǒng)的分析增值活動與浪費,然后持續(xù)的推進改善;并希望建立一個機制,能夠定期重復進行價值流分析。
這其實是一種廣義的價值流管理了。博革咨詢是不太贊成這種思路的。博革咨詢認為企業(yè)的各項管理流程有不同的適用工具,將“價值流圖”這個工具應用于運營管理的全流程診斷是不合適的,企業(yè)應該根據面臨的問題合理選擇工具包。
價值流圖這個工具最初導入時主要適用于離散制造車間的交付周期和在制品分析,用于縮短交期,降低在制品庫存。后面進一步拓展到公司層面,將客戶訂單下達,主生產計劃和供應商交付的內容也一并納入。然后將制造價值流圖稱為“車間級價值流圖”,包含計劃和采購內容的價值流圖稱為“公司級價值流圖”。此時這個工具已經有些力不從心了,博革咨詢見過大多數企業(yè)繪制的公司級價值流圖其實并沒什么大的用處。如果希望進行深入分析還需要導入不同的工具。
分析計劃交付流程可以用“結合MRP理論的變量流程圖法”;“SCOR參考模型”“供應鏈伙伴關系模型”三種方法;
分析總裝線效率更適合用LOB方法;
分析關鍵資源效率可以用OEE瀑布圖;
分析設施布局可以用“產品布置原則”;
分析現(xiàn)場浪費可以用“七大浪費改善巡查”
分析過程質量可以用PFMEA和QC工程表
即使是車間級價值流圖,很多公司使用的也不恰當,效果也不大。價值流圖繪制一般都是按照周改善的方式推進,成立跨部門的小組,繪制當前的價值流圖,找出庫存積壓點,關鍵資源的切換頻次和切換周期;設備的利用率等數據。然后頭腦風暴列出改善點,定義未來的價值流目標,其實就是目標車間在制庫存水平和交付周期。這個目標庫存水平和交付周期往往是領導硬拍下來的,例如當前交付周期降低30%。 雖然活動很熱鬧,大家很激動,但最終收效很小。十幾年前,博革咨詢在飛思卡爾作為精益專員也是在顧問的指導下這么干的。當時博革咨詢對美國那個顧問提出疑問,封裝周期縮短1天,測試周期縮短2天,意義何在?當時顧問的回答是通過縮短在制品庫存可以減少車間面積占用,更好的響應客戶需求,節(jié)約資金占用。
博革咨詢分析下來:公司的原材料和成品庫存才是大頭,車間節(jié)約的這1-2天庫存,折算成利息,一年幾十萬的成本,還不如幾臺設備提升OEE來的更多;至于快速客戶響應,對于緊急訂單,公司都是安排專人跟進,周期遠遠短于改善目標。至于車間面積占用,半導體是高值產品,一天的產量一個手推車就放下了。
后面做了咨詢,才意識到,車間價值流分析主要是解決2個點:解決從客戶需求分解下來的車間交期目標;解決車間面積不足的問題。
從客戶需求開始,反推出各車間的交付目標。然后利用價值流圖這個工具來解決交期。
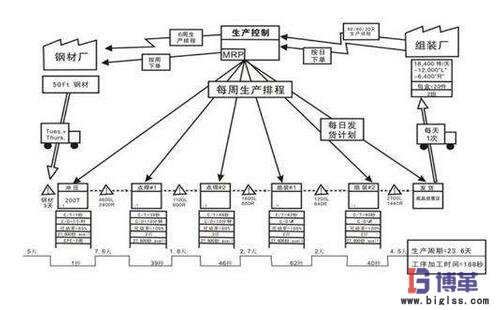
這其實是一種廣義的價值流管理了。博革咨詢是不太贊成這種思路的。博革咨詢認為企業(yè)的各項管理流程有不同的適用工具,將“價值流圖”這個工具應用于運營管理的全流程診斷是不合適的,企業(yè)應該根據面臨的問題合理選擇工具包。
價值流圖這個工具最初導入時主要適用于離散制造車間的交付周期和在制品分析,用于縮短交期,降低在制品庫存。后面進一步拓展到公司層面,將客戶訂單下達,主生產計劃和供應商交付的內容也一并納入。然后將制造價值流圖稱為“車間級價值流圖”,包含計劃和采購內容的價值流圖稱為“公司級價值流圖”。此時這個工具已經有些力不從心了,博革咨詢見過大多數企業(yè)繪制的公司級價值流圖其實并沒什么大的用處。如果希望進行深入分析還需要導入不同的工具。
分析計劃交付流程可以用“結合MRP理論的變量流程圖法”;“SCOR參考模型”“供應鏈伙伴關系模型”三種方法;
分析總裝線效率更適合用LOB方法;
分析關鍵資源效率可以用OEE瀑布圖;
分析設施布局可以用“產品布置原則”;
分析現(xiàn)場浪費可以用“七大浪費改善巡查”
分析過程質量可以用PFMEA和QC工程表
即使是車間級價值流圖,很多公司使用的也不恰當,效果也不大。價值流圖繪制一般都是按照周改善的方式推進,成立跨部門的小組,繪制當前的價值流圖,找出庫存積壓點,關鍵資源的切換頻次和切換周期;設備的利用率等數據。然后頭腦風暴列出改善點,定義未來的價值流目標,其實就是目標車間在制庫存水平和交付周期。這個目標庫存水平和交付周期往往是領導硬拍下來的,例如當前交付周期降低30%。 雖然活動很熱鬧,大家很激動,但最終收效很小。十幾年前,博革咨詢在飛思卡爾作為精益專員也是在顧問的指導下這么干的。當時博革咨詢對美國那個顧問提出疑問,封裝周期縮短1天,測試周期縮短2天,意義何在?當時顧問的回答是通過縮短在制品庫存可以減少車間面積占用,更好的響應客戶需求,節(jié)約資金占用。
博革咨詢分析下來:公司的原材料和成品庫存才是大頭,車間節(jié)約的這1-2天庫存,折算成利息,一年幾十萬的成本,還不如幾臺設備提升OEE來的更多;至于快速客戶響應,對于緊急訂單,公司都是安排專人跟進,周期遠遠短于改善目標。至于車間面積占用,半導體是高值產品,一天的產量一個手推車就放下了。
后面做了咨詢,才意識到,車間價值流分析主要是解決2個點:解決從客戶需求分解下來的車間交期目標;解決車間面積不足的問題。
從客戶需求開始,反推出各車間的交付目標。然后利用價值流圖這個工具來解決交期。
作者:老麥